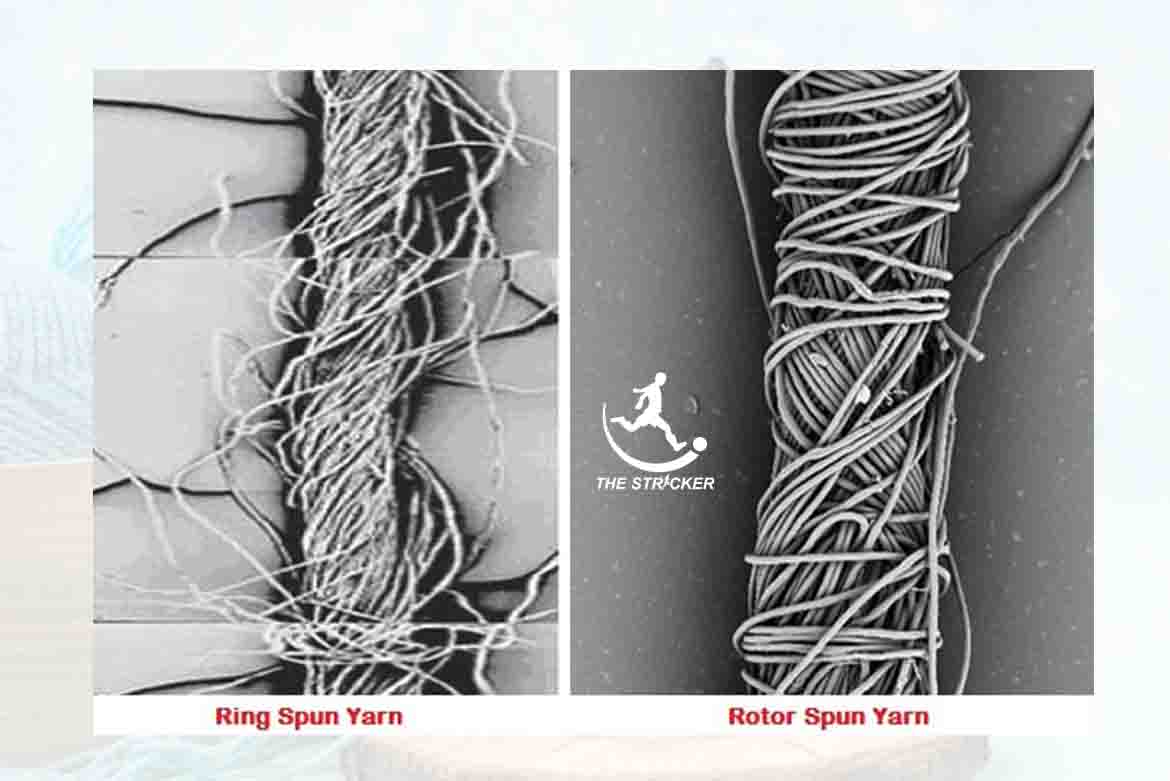
Ring Yarn is known as Ring Spun Yarn and Rotor Yarn is known as Rotor Spun Yarn. We will discuss Ring Yarn Vs Rotor Yarn in this article.
Ring Yarn Vs Rotor Yarn
Ring-spun yarn:
ring-spun yarn is made by twisting and thinning the cotton strands to make a very fine, strong, soft rope of cotton fibers. Most yarns made from staple fibers are ring-spun yarns. The twist that provides the final entanglement is built up from the outside to the inside. Although a high quality ring yarn first appears to be as uniform as a filament, closer microscopic examination would reveal a uniform helical arrangement of fibers at the surface, as shown in Fig. Ring-spun yarn are more durable and last longer than their regular counterparts, but will also be more expensive, too.
Properties of ring-spun yarns:
Tensile properties:
Elongation and breaking strength are two important quality attributes of any spun yarn. The strength of a staple yarn is determined by various fiber properties, the yarn structural geometry and the spinning parameters.
Mass irregularity and imperfections:
Another important quality parameter of the yarn is its mass unevenness along its length. This unevenness is the result of the variation in the number of fiber ends per unit length. The important measures that can reduce yarn irregularity and associated imperfections are (1) individualization of fibers, (2) minimization of inter-fibre contact by greater fiber parallelization, and (3) control on the movement of short fibers.
Hairiness:
Hairiness is a property which indicates the amount and length of fiber ends and loops protruding from the body of the yarn. It is a desirable property in certain situations and undesirable in other circumstances, depending upon the type of end-use and application of the resultant fabric.
Factors affecting yarn properties:
Fiber factors:
Although several experimental investigations concerning the strength and elongation of staple yarns have been reported in the literature, it is important to know the order in which the fibre and other parameters affect yarn strength, so that appropriate attention may be paid to these factors during the selection of the raw materials and processing parameters. Usually the strength translation efficiency from fiber to yarn is 40–65%.
Yarn hairiness is another important quality attribute affected by the fiber parameters. Fiber fineness has the maximum influence on the hairiness, and is followed by fiber length.
Yarn factors:
As the linear density of a yarn is reduced, the yarn strength is also reduced because of the lower number of fibers in the yarn cross-section.
Machine factors:
Yarn hairiness can be regulated by selecting the ring frame draft and spindle speed. For a constant yarn count, hairiness increases with increase in these two factors. Increased spinning tension also increases yarn hairiness. High production carding, chemical processing of fibers prior to spinning, poor ring frame conditions due to traveller flutter, and high levels of humidity can also cause excessive hairiness.
End uses of ring-spun yarns:
The ring spinning system can be used to produce very coarse to extremely fine yarns with a very large range of twist density from various types of fibers and their blends. ring-spun yarns can therefore be engineered to impart the desired hand, e.g. crispness or softness, to a fabric according to requirements. ring-spun yarns are widely used for shirts, trousers, nightwear, blouses, overalls, suits, skirts, sheeting, curtaining and other industrial textiles.
Ring Yarn Vs Rotor Yarn
Rotor Spun Yarn:
Rotor spun yarn is less strong than comparable ring-spun yarn. This is because of the straight, parallel arrangements of fibers and denser packing of fibers in the ring-spun yarn which contrast with the higher numbers of disoriented folded fibers in rotor spun yarn, lower levels of fiber migration, less packing and the presence of non-load bearing wrappers and belt fibers. Rotor spun yarns are generally more extensible than ring-spun yarns.
Properties of rotor spun yarns:
Rotor spun yarns appear to be no different from ring-spun yarns on the surface. However, there exist some rather important differences in the internal structures of the yarns, especially in fiber contiguity. These differences in internal structures are reflected in different performance characteristics. Rotor spun yarns tend to be more uniform in appearance and in linear density than ring-spun yarns. It is conceivable that the better short-term evenness of rotor spun yarn is an obvious result of the suppression of the drafting wave and the large packages formed in rotor spinning. Also, rotor spun yarns are known to be somewhat more extensible, fuller, softer and less hairy. The main disadvantage is that rotor spun yarns are not as strong as ring-spun yarns, and the maximum tenacity of rotor spun yarns is at least 10–30%, and in some cases even up to 40%, lower than that of ring-spun yarns. It is pointed out that although significant differences exist between the rotor and ring-spun yarns, various fiber factors and spinning conditions could greatly alter the properties of rotor spun yarns.
Factors affecting yarn properties:
Fiber parameters:
The choice of raw material plays a dominant role in controlling yarn quality in rotor spinning. There is a general consensus of opinion that the raw material properties must be ranked in a different order of importance for rotor spinning than for ring spinning.
Fiber length characteristics, particularly length uniformity, play only a minor role in rotor spinning, and long fibers offer no advantage. Longer fibers can adversely affect yarn strength and evenness due to the greater incidence of wrapper fibers and poor fiber orientation.
Sliver quality:
The quality of feed sliver in terms of cleanliness, uniformity and orientation of fibers has a profound influence on end breaks in rotor spinning and consequently on the rotor yarn properties such as strength and irregularity. Sliver variations cause an uneven flow of fibers through the transport duct and their subsequent deposition in the rotor groove, which, in turn, results in yarn count variation and poor spinning performance.
It is important to maintain high fiber orientation in the drafted sliver, since this leads to a more ordered arrangement of fibres in the rotor groove, which facilitates easy flow of twist along the rotor periphery and improves spinning stability and yarn strength.
Rotor machine variables:
While producing thick sliver, the question of high total draft inevitably crops up. Increasing total spinning draft leads to an increased end-breakage rate and deterioration in the tenacity, breaking elongation and uniformity of the spun yarn. The opening roller is a key parameter influencing rotor spun yarn characteristics. It individualizes the fibers and thereby assists in feeding them to the rotor.
End uses of rotor spun yarns:
Rotor spinning can be employed to spin good quality yarns of 18–200 tex from cotton, polyester blends, viscose rayon and acrylic fibers. From microfibers, it is now quite possible to spin yarns down to 10 tex. The products for which rotor spun yarns are considered particularly suitable include dress materials, denim and jeans, sheeting, leisure wear, industrial wear, interlining, towels, furnishings and warp knits.
Comparison of ring-spun and Rotor Spun Yarns:
There are many difference between ring and rotor spun yarns. The abrasion resistance of rotor yarn fabrics is better, and color fastness is slightly higher for ring-spun yarn fabrics whereas shrinkages is the same for the fabrics made from ring & rotor spun yarns. Two of the important differences are the degree of fiber hookiness and fiber migration. In below table there are given many difference between ring and rotor spun yarns.
Table: Difference between ring and rotor spun yarns
Characteristics of yarns | Spinning method | |
ring-spun yarn | Rotor spun yarn | |
Production rate | High | Higher |
Tenacity | Very high | Average |
Linear density | 5–600 tex | 20–60 tex |
Twist | Lower | Higher |
Extensibility | Average | Higher |
Abrasion resistance | Lower | Higher |
Strength variation | High | Low |
Yarn faults | High | Reduced by 80% |
End breaks | High | Reduced by 75% |
Fly liberation | High | Less |
Neppiness | Higher | Lower |
Hairiness | Very high | Lower |
Regularity | Lower | Higher |
Handle | Softer | Harsher |
Appearance | Less uniform | More uniform |
Fiber blending | Lower | Higher |
Wrapper fibers | None | Present |
Ring Yarn Vs Rotor Yarn
Conclusion
The following conclusion can be drawn from this study.
1. Tensile and tearing strengths are more when the fabric is tested along the ring-spun yarn direction than along the rotor spun yarn direction. This is mainly due to the lower yarn strength of the rotor yarns.
2. The breaking elongation is less for rotor spun yarn.
3. Bending length is same for the fabrics made from ring and rotor spun yarn.
4. Fabric thickness is high when the proportion of rotor yarn in the fabric is more, and this is because of higher bulk of rotor spun yarn.
5. Crease recovery and air permeability is slightly poor for the fabrics made from ring-spun yarn as compared to the rotor spun yarn fabrics.
6. Drape coefficient percentage is slightly higher for the ring-spun yarns.
7. Abrasion resistance of rotor yarns is better than ring yarns due to the wrapper fibres which have mobility on the yarn core and thus avoid abrasion with the abradent.
8. Colour fastness is slightly higher for ring-spun yarns fabric whereas shrinkage is the same for the fabrics made from ring and rotor spun yarns.
You May Also Read: