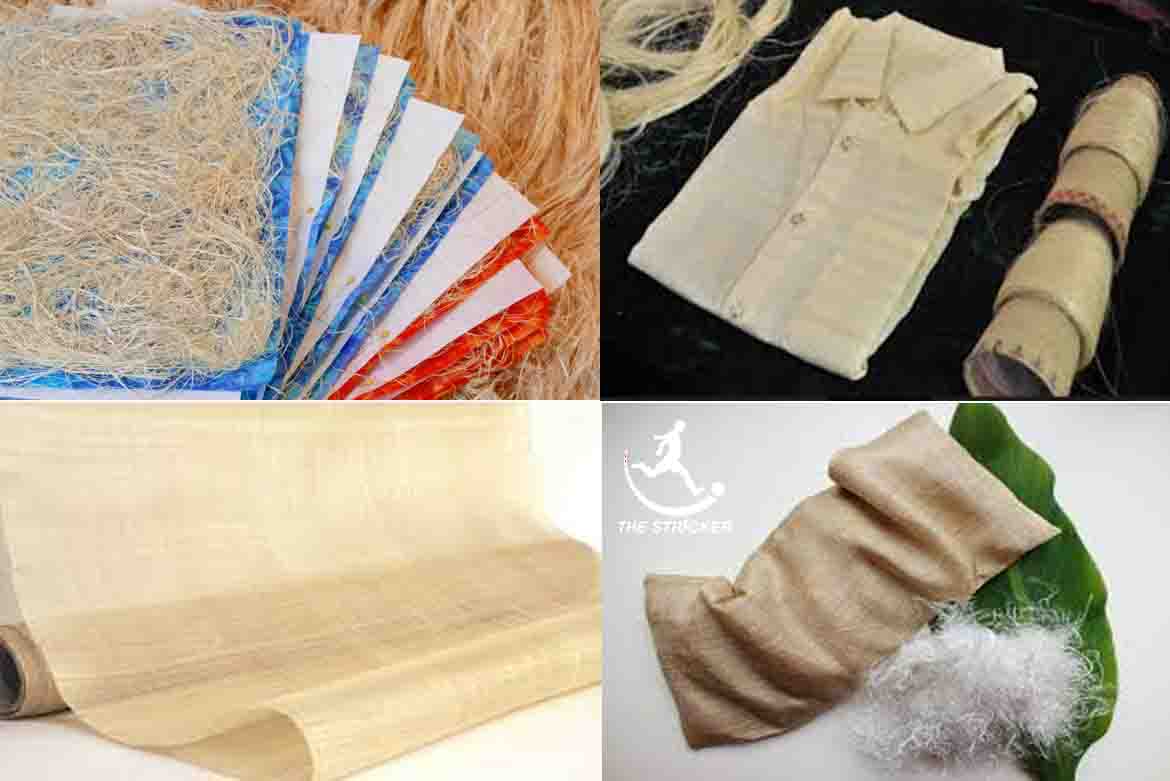
Natural fibers have been used historically to produce our clothes’ carpets, cordage, paper, ship sails and insulation, and building materials. In this article’ we will discuss Banana Fiber; Properties of Banana Fiber’ Uses of Banana Fiber. Along with the History and Production Process.
What is Banana Fiber?
Is it a Bast Fiber?
Banana fiber is a natural fiber. It is a lignocellulosic fiber. It is obtained from the pseudo-stem of the banana plant (Musa sepientum). So it is a bast fiber.
It can be blended easily with cotton fiber or other synthetic fibers to produce blended fabric & textiles.
The use of banana stems as a source of fiber declined after other convenient fibers such as cotton and silk became popular. But in recent years the commercial value of banana fiber has increased and it is used all over the world for multiple purposes from making tea bags and sanitary napkins to Japanese yen notes and car tires.
History
According to archaeologists; the banana was first domesticated in the Kuk valley of New Guinea around 8,000 BCE. Though this is the first known location of banana domestication; other spontaneous domestication projects may have occurred throughout South East Asia and the South Pacific.
Historically, banana stems had been used as a source of fiber with the earliest evidence dating to the 13th century. But its popularity faded after other convenient fibers such as cotton and silk were made popular. For centuries, banana fiber textiles were made in Japan and Nepal.
Characteristics
- Natural sorbent: Fabric from theses fibers lets you breathe well and will keep you cool on hot days.
• Soft, supple, and shimmer: Banana fabric is soft and supple; though not quite as soft as cotton or rayon. Nearly all plant stem-based fibers are a little more stiff and coarse than cotton or rayon. Its natural shimmer makes it look a lot like silk.
• Comfort: Banana fiber clothing is comfortable and not likely to trigger allergies.
• Biodegradable.
• Resistance: It is grease-proof, water-, fire- and heat-resistant.
• Durability: Even if the banana fabric is made from the tough outer sheath, it is not as strong and durable as any fabric like hemp, bamboo, or other natural fiber.
• Insulation: It is not particularly insulating.
• Spin ability and tensile strength: It is better than other organic fibers in terms of spin ability and tensile strength.
What makes banana fibers special?
- Banana fiber is a good alternative to all the synthetic and natural fibers.
- Banana fiber is eco-friendly, chemical-free, non-toxic, and odor-free.
- The natural coolant and medicinal property of banana fibers help in the health of its user and is 100 percent safe as no harmful chemicals and colors are used.
Fiber Properties
Tenacity | 29.98 g/denier |
Fitness | 17.15 denier |
Moisture regain | 13 percent |
Elongation | 6.54 |
Alco-ben extractives | 1.70 percent |
Total cellulose | 81.8 percent |
Alpha cellulose | 61.5 percent |
Residual Gum | 41.9 percent |
Lignin | 15 percent |
Application and Uses
Organic banana fiber is used to make various eco-papers like tissue, filters, and currency paper. Being natural, heat resistant; having a good spinning ability, and high tensile strength; it is used for making yarn, fabrics, and garments. It can be blended with other fibers.
Eco-friendly bags are made from banana fiber. Banana fiber paper can be a substitute for polythene bags.
It has high nutrition content to nurture the growth of plants/crops. It increases production or yield and gives organic output, which is very beneficial.
Banana fiber cloth is eco-friendly. Clothes made from banana fiber have a silk-like feeling and do not require any chemicals to make.
Sanitary napkins from banana fibers
The International Institute for Environment and Development has even launched a program to educate women in Rwanda in making low cost and environmentally friendly sanitary pads out of banana fibers.
Use of banana fiber in Japanese yen notes
During the research, it was found that the paper made out of this fiber has a shelf life of over 100 years and it can be folded as many as 3,000 times. The fiber has the potential to find application in the making of paper for printing currency.
Use of banana fibers in making tea bags
Teabag paper is made primarily from abaca hemp, a product of a Philippine banana tree that is also known as Manila hemp. This is bleached and processed and then treated with a heat-sealable thermoplastic such as PVC or polypropylene on the inside. Banana paper is much stronger than regular paper. It is used for cement bags to carry up to 25 kilograms and other heavy-duty bags. Since the tenacity of banana fiber is high, some automobile companies use it to reinforce the body of the vehicle.
Use of banana fibers in car tires
The second-generation Mercedes-Benz A class designed the spare tire recess covered with a composite material, polypropylene, thermoplastic with embedded banana fibers, with high tensile strength and rot resistance. It can withstand stone strikes and exposure to the environment, such as UV from the sun, water, some chemicals.
Revolution in the Fiber industry
The banana fiber separator machine created this revolution. The separator is one of the innovative ventures incubated at TREC-STEP; India, which uses the agricultural waste of banana harvests to produce silk grade fiber for local handicrafts and textile industries. What was previously regarded as agricultural waste and a nuisance for farmers is now a raw material for good quality silk grade fiber yarn. TREC-STEP gives us an insight into this innovative venture.
The entrepreneur behind this venture, Mr. K. Murugan, a mechanical engineer by training, designed and produced the machine to extract valuable parts of the remaining pseudostem of banana harvests into a commercially viable product.
He was originally attracted by the shiny texture of the banana fiber that was left over after harvesting and began to wonder whether a refined form of this could replace the rich silk fabric his mother often used. After many trials with a resourceful mechanic, he developed a crude machine for extracting banana fiber and ended up with products such as silk yarn and silk zari, new and unrivaled products on the market. It took nearly 12 years of study and research, and 40 trials with various extraction machine models, before Murugan and his colleague managed to produce a successful prototype and arrive at the current version of the banana fiber separator machine.
There are numerous potential clients for organic banana fabrics. The realization of this client’s potential depends on the market penetration strategy. Presently there are huge exports potential and orders are available on hand.
Production
Harvest
Cut 1 to 1.5 meter long pieces of banana fiber from the garden early in the morning or late in the evening when it is soft. If it is picked when it is too dry, it rips apart during preparation.
2. Clean fiber
Wipe the banana fiber with a damp cloth to remove dirt.
3. Straighten fiber
Hold fiber with one hand and with your other hand gently, but firmly; pull your palm along the length of fiber from one end of the fiber to the other.
4. Peel fiber
Carefully peel off the waterproof layer from the surface of fiber (the “Intestine layer”) that will lie against the skin.
5. Cracked fibers
If the fiber cracks near the middle, it cannot be used. If it cracks near edge; tear off the cracked edge (as long as remaining width is sufficient for user.)
6. Fiber ready to use:
The fiber is ready for use once the waterproof layer that will lie against the skin is completely peeled off.
Sources:
You May Also Read: