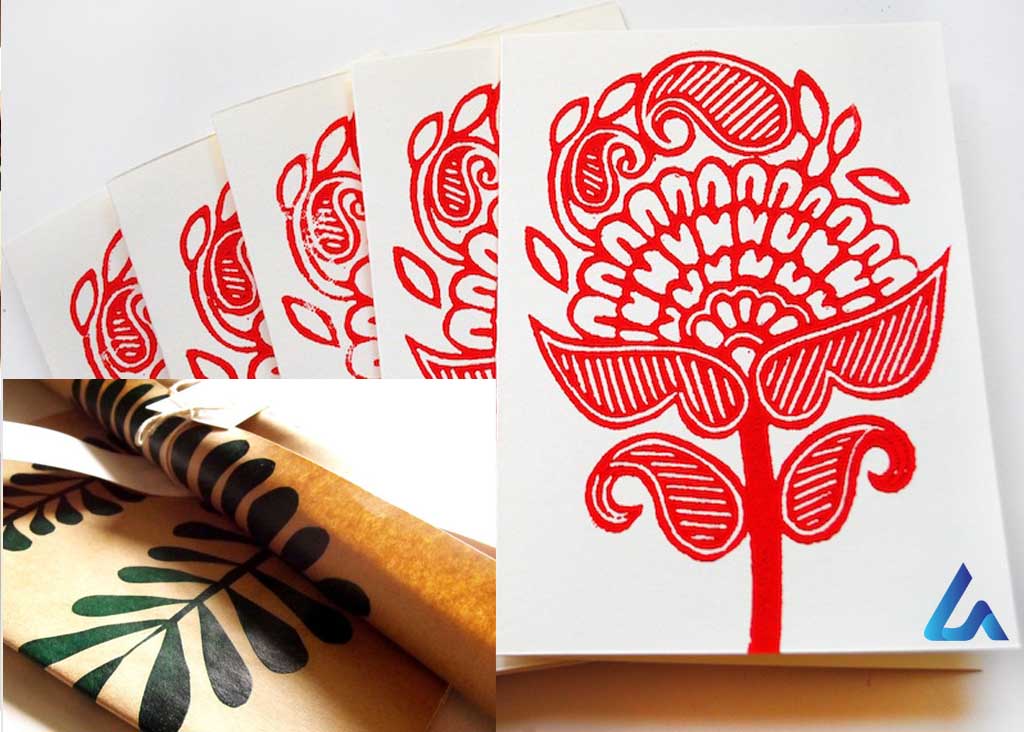
Introduction
Block printing is a method of printing textiles by stamping ink-dipped blocks—usually made from wood or linoleum—onto fabric. This technique is one of the simplest ways to create custom fabric at home.
In this article, we will try to answer;
-
What is block printing?
-
History of block printing
-
Types of Block Printing in India
-
block print techniques
-
Basic Materials for Block Printing Fabric
-
How to Bock Print on Fabric
-
Why was block printing important?
From the introduction; we already know what Block Printing is. So let’s know the origin and history of the process.
Block Printing History
Woodblock printing or block printing is a technique for printing text; images or patterns. It was used widely throughout East Asia and originating in China; in antiquity as a method of printing on textiles and later paper. As a method of printing on cloth; the earliest surviving examples from China date to before 220 AD.
Different Types of Block Printing in India
India is known for its unique arts and crafts. Different types of hand printing techniques are used in this country by people of varied customs and culture.
The major centers in India where block printing is done on large scale are as follows:-
– Gujarat (Surat, Ahmedabad, Sanganer, Pethapur).
– Rajasthan (Bagru).
– Andhra Pradesh.
– Uttar Pradesh (Farukhabad).
– West Bengal.
Since the ancient time; Block Printing is done in different techniques. We will discuss the top 3 techniques of woodblock printing.
Techniques of Hand Block printing
1) Discharge Printing
Firstly the fabric on which printing is to be done is dyed. The dye is removed from the part of the fabric on which designs are to be made by use of a chemical. Then those segments printed are treated so that they can be re-colored.
2) Direct Block Printing
The fabric used here is either cotton or silk. The cloth is first bleached and then dyed with the desired color. After that block printing is done on borders with carved wooden blocks then inside the borders.
3) Resist Printing
In this technique, the part of the cloth which is not to be dyed is covered with the paste of resin and clay. Then the fabric is dyed with the desirable color; at this stage, the dye penetrates through the cracks which creates a wavy effect of colors on the cloth. After this, the fabric is finally block printed.
Basic Materials for Block Printing Fabric
- block printing carving block
- fabric block printing ink OR water-soluble printing ink for paper
- linoleum cutter carving tool
- soft rubber brayer
- acrylic sheet, glass (or similar)
- permanent marker
How to Block Print Fabric
Step 1: Create a design and draw it onto your linoleum block.
The first step for block printing is coming up with a design. Use a permanent marker to draw the design directly onto the carving block. That way, you know exactly what to cut and what you don’t want to cut. It really helps to have a visual guide.
You want to use a permanent marker, as opposed to any other kind of marker or pen. This will ensure the ink from the marker doesn’t come off onto your fabric or paper while printing.
Step 2: Get familiar with your tools and know when to use what attachments, etc.
Next, using your carving tools, choose the size lino cutter attachment you want to use.
I often use the largest size to carve out larger areas, so it goes a little faster. In the carving tool I have linked the largest size it comes with is a #5 and the smallest size is a #1. But for highly detailed areas, you’ll probably want to use the smallest size
Additionally, you can use the knife blade tool (labeled #6 for the tool I linked) to carefully cut around the edges of a design. This would be especially helpful if you’re concerned about messing up and carving too closely into something. A great thing to do for beginners.
It creates more of a guide to follow and a stopping point for the other attachments to help with those fine lines, etc. And it can also be used to cut away excess material from the side of the block to make it easier to handle while stamping.
Side note: These blades and cutting attachments are very sharp! So use caution with the carving tools and always be aware of how close your fingers and hands are to the blade. Also, be aware of fingers that are holding the linoleum block in place opposite the tool. It is always possible to lose control of your carving tool. Basically, just be careful.
Step 3: Start carving the linoleum block.
Based on what you learned in step two, select the best attachment. Then, begin cutting out the excess area away from the design. Leaving the design raised, as shown in the photo. Use as many of the different size options as you find necessary, depending on your design.
Step 4: Ink your linoleum block.
If you’re block printing on fabric, you’ll want to use a block printing ink that is safe to use on fabrics. It will say it’s for fabric use right on the tube, like this one for example.
Another option for block printing fabric is using an ink pad that can be used on fabrics, like this one. Using ink pads for block printing are best for small lino blocks (2-3 inches in size).
If you’re using larger blocks, you’ll probably want to go the traditional route of inking, which I’ll explain below.
*Also, this method of using an ink pad isn’t really a true form of block printing. BUT it is a nice option when you’re in a hurry, or want to save money with the purchase of a few less tools.
If you’re using a fabric ink pad and small linoleum block, open up the ink pad and continuing dabbing ink onto the lino block until the design is fully (and evenly) covered.
If you’re using a more traditional method for inking, squeeze out a thin line of ink (whether its fabric ink or regular printing ink for paper) toward the top of the acrylic sheet (or glass) palette.
Then use the soft rubber brayer (the roller), to bring the ink down. Rolling the ink out a bit on the surface of your palette before rolling it over your stamp in thin layers until the raised design is fully covered. Make sure the linoleum block isn’t over inked or you could lose some of the fine details of your design when printing.
You’ll notice when you roll the ink out that it has a much different viscosity than regular paint. It’s much tackier.
Step 5: Print block design onto fabric (or paper).
Next, no matter how you’ve inked your lino block, flip the block over. Then press the inked design face down firmly and evenly onto fabric or paper. Then, pull the stamp away from the fabric, straight up if you can.
Repeat steps 4 and 5 as desired. If you’re using traditional block printing ink, let the surface air dry for 24 hours before using (this will set the ink). Or according to instructions on the ink tube. As some inks require more time to cure.
OR if you’re using a fabric ink pad, wait for the pattern to air dry, then heat set the ink (with an iron) to ensure the ink is permanent.
Importance Of Block Printing
In this age where machines churn out yards of fabric limitations, here is a product that is created by hand with utmost skill and care. This factor alone is sufficient to mark the uniqueness of this technique. However, as another special quality that few other designs can replicate. The technique has evolved over centuries, but most of the original methods remain intact, and each hand block printed fabric has its unique story to tell.